Warm forging and thermoforming applications
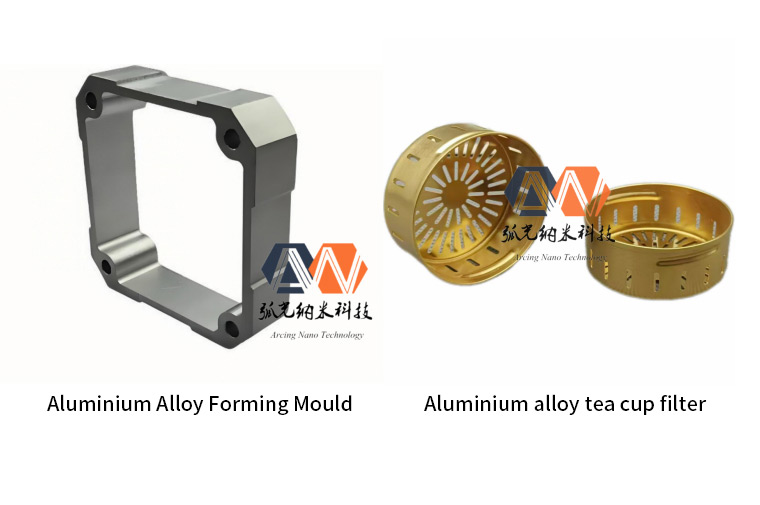
The application of PVD coating technology in the life extension of hot forging dies is through the use of PVD coating technology, such as Diamond Like Coating (DLC), Titanium Nitride Coating (TIN), Aluminium Chromium Nitride Coating (AlCrN), etc., to enhance the properties of the dies such as abrasion and corrosion resistance, low coefficient of friction and so on, thus prolonging the service life of the dies. These coating technologies are used in a wide range of applications, including but not limited to precision parts, plastic moulds, cutting tools, etc. Especially in the application of hot forging moulds, they can significantly improve the durability of the moulds and reduce the maintenance cost, which in turn improves the production efficiency.
1) Diamond Coating (DLC): with high lubricity (low coefficient of friction) and oil-free self-lubricating performance, it is suitable for precision parts in the fields of automation fittings, new energy battery equipments, automotive parts and so on.
2) Titanium Nitride Coating (TIN): it is the most typical and universal PVD superhard coating, mainly used for wear-resistant coatings for turning, milling, drilling and gear tools and anti-adhesion, improved lubrication and wear-resistant protective coatings for moulding and injection moulds.
(3) Aluminium chromium nitride coating (AlCrN): with extremely high oxidation resistance and thermal hardness, it is suitable for high-temperature alloys as well as turning and milling of hard-to-cut materials and high-speed cutting of gear processing, and it is also suitable for the coating of thermoforming, hot forging moulds and die-casting moulds.
The application of these PVD coating technologies not only improves the service life of moulds and tools, but also broadens their application areas, especially in warm and hot forging and hot forming applications, which bring significant economic benefits to industrial enterprises by reducing maintenance costs and improving productivity.